Hardware specification¶
Note
The following hardware specifications are provided here as a general reference; differences with the product may exist.
Scope of delivery¶
Standard delivery for an rc_visard NG includes the rc_visard NG sensor and a quickstart guide only. The full manual is available in digital form and is always installed on the sensor, accessible through the Web GUI, and available at https://roboception.com/resources/knowledge-base/.
Note
The following items are not included in the delivery unless otherwise specified:
- Couplings, adapters, mounts
- Power supply unit, cabling, and fuses
- Network cabling
Please refer to Accessories for suggested third-party cable vendors.
A connectivity kit can be purchased for the rc_visard NG. It contains an M12 to RJ45 network cable, 24 V power supply, and a DC plug to M12 power adapter. Please refer to Accessories for details.
Note
The connectivity kit is intended only for initial setup, not for permanent installation in industrial environment.
The following picture shows the important parts of the rc_visard NG which are referenced later in the documentation.
Technical specification¶
The technical specifications for the rc_visard NG are given in Table 1. The frame rate for computing the depth image in High resolution (720 x 540 pixel) is significantly higher when increasing the minimum distance to 1.2 meters.
rc_visard NG 160-6 | |
---|---|
Image resolution | 1440 x 1080 pixel, monochrome |
Field of view | 6 mm lens: Horizontal: 43°, Vertical: 33°
|
IR Cutoff | 650 nm |
Depth image (with Minimum
|
1440 x 1080 pixel (Full) @ 3 Hz
720 x 540 pixel (High) @ 7 Hz
360 x 270 pixel (Medium) @ 25 Hz
240 x 180 pixel (Low) @ 25 Hz
|
Depth image (with Minimum
|
1440 x 1080 pixel (Full) @ 3 Hz
720 x 540 pixel (High) @ 16 Hz
360 x 270 pixel (Medium) @ 25 Hz
240 x 180 pixel (Low) @ 25 Hz
|
Computing unit | Orin Nano 8GB |
Power supply | 18 V to 30 V |
Cooling | Passive |
Baseline | 160 mm |
Depth range | 0.5 m to infinity |
Size (W x H x L) | 230 mm x 75 mm x 84 mm |
Mass | 0.965 kg |
The resolutions and accuracies at different distances are given in the following table.
distance (mm) | rc_visard NG 160-6 | |
---|---|---|
lateral resolution (mm) | 500
1000
2000
3000
|
0.3
0.6
1.1
1.7
|
depth resolution (mm) | 500
1000
2000
3000
|
0.05
0.2
0.9
2.0
|
Average depth accuracy (mm) | 500
1000
2000
3000
|
0.2
0.9
3.5
7.8
|
The rc_visard NG can be equipped with on-board software modules for additional features. These software modules can be ordered from the Roboception and require a license update.
CAD models of the rc_visard NG can be downloaded from http://www.roboception.com/download. The CAD models are provided as-is, with no guarantee of correctness. When a material property of aluminum is assigned (density of \(2.76\mathrm{g\over{cm}^3}\)), the mass properties of the CAD model are within 5% of the actual product with respect to weight and center of mass, and within 10% with respect to moment of inertia.
Environmental and operating conditions¶
The rc_visard NG is designed for industrial applications. Always respect the storage, transport, and operating environmental conditions outlined in Table 3.
rc_visard NG | |
---|---|
Storage/Transport temperature | -25 °C to 70 °C |
Operating temperature | 0 °C to 50 °C |
Relative humidity (non condensing) | 20 % to 80 % |
Vibration | 5 g |
Shock | 50 g |
Protection class | IP54 |
Others |
|
The rc_visard NG is designed for an operating temperature (surrounding environment) of 0 °C to 50 °C and relies on convective (passive) cooling. Unobstructed airflow, especially around the cooling fins, needs to be ensured during use. The rc_visard NG should only be mounted using the provided mechanical mounting interface, and all parts of the housing must remain uncovered. A free space of at least 10 cm extending in all directions from the housing, and sufficient air exchange with the environment is required to ensure adequate cooling. Cooling fins must be free of dirt and other contamination.
The housing temperature depends on the processing load, sensor orientation, and surrounding environmental temperatures. When the sensor’s exposed housing surfaces exceed 60°C, the LED at the front will turn from green to red.
Warning
For hand-guided applications, a heat-insulated handle should be attached to the sensor to reduce the risk of burn injuries due to skin exposure to surface temperatures exceeding 60°C.
Power-supply specifications¶
The rc_visard NG needs to be supplied by a DC voltage source. The rc_visard NG’s standard package doesn’t include a DC power supply. The power supply contained in the connectivity kit may be used for initial setup. For permanent installation, it is the customer’s responsibility to provide suitable DC power. Each rc_visard NG must be connected to a separate power supply. Connection to domestic grid power is only allowed through a power supply certified as EN55011 Class B.
Min | Nominal | Max | |
---|---|---|---|
Supply voltage | 18.0 V | 24 V | 30.0 V |
Max power consumption | 25 W | ||
Overcurrent protection | Supply must be fuse-protected to a maximum of 2 A |
Warning
Exceeding maximum power rating values may lead to damage of the rc_visard NG, power supply, and connected equipment.
Warning
A separate power supply must power each rc_visard NG.
Warning
Connection to domestic grid power is allowed through a power supply certified as EN55011 Class B only.
Wiring¶
Cables are not provided with the rc_visard NG standard package. It is the customer’s responsibility to obtain the proper cabling. Accessories provides an overview of suggested components.
Warning
Proper cable management is mandatory. Cabling must always be secured to the rc_visard NG mount with a strain-relief clamp so that no forces due to cable movements are exerted on the rc_visard NG’s M12 connectors. Enough slack needs to be provided to allow for full range of movement of the rc_visard NG without straining the cable. The cable’s minimum bend radius needs to be observed.
The rc_visard NG provides an industrial 8-pin A-coded M12 socket connector for Ethernet connectivity and an 8-pin A-coded M12 plug connector for power and GPIO connectivity. Both connectors are located at the back. The location of both connectors on the rc_visard NG is shown in Fig. 4.
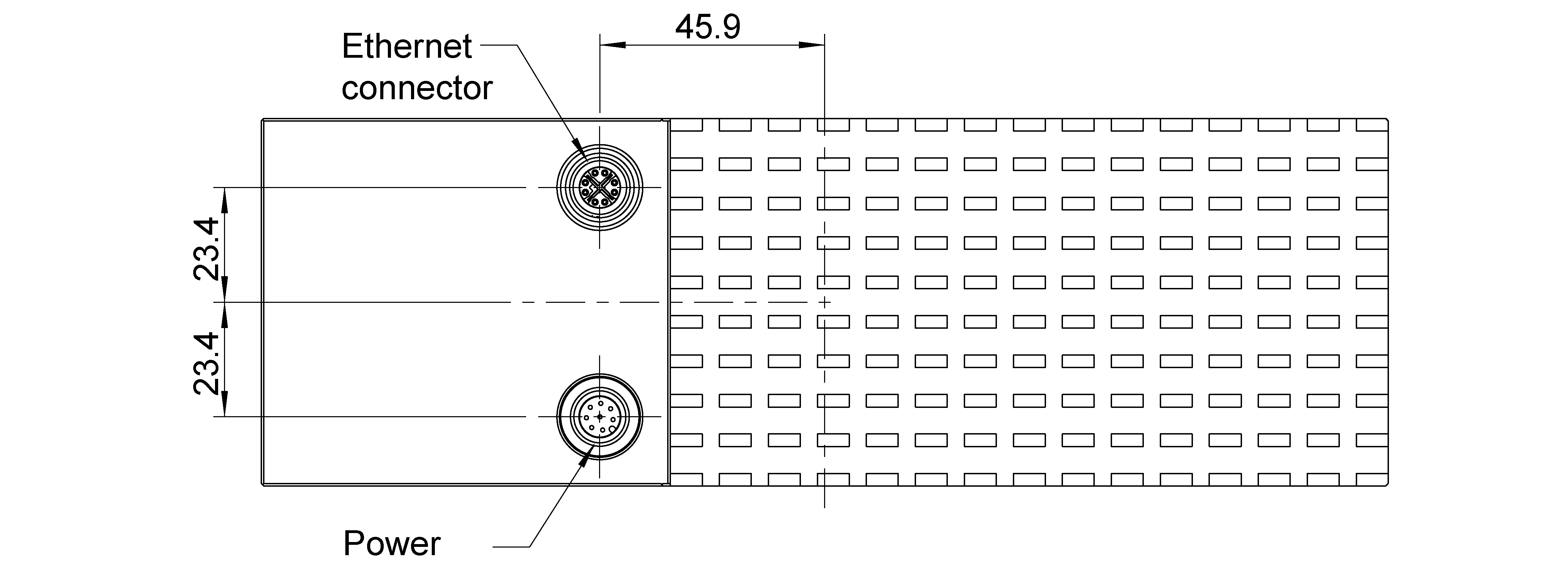
Fig. 4 Locations of the electrical connections for the rc_visard NG, with Ethernet on top and power on the bottom
Connectors are rotated so that standard 90° angled connectors will exit horizontally, away from the camera (away from the cooling fins).
Pin assignments for the Ethernet connector are given in Fig. 6.
Pin assignments for the power connector are given in Table 5.
Pin | Assignment |
---|---|
1 | GPIO In 2 |
2 | Power |
3 | GPIO In 1 |
4 | GPIO Gnd |
5 | GPIO Vcc |
6 | GPIO Out 1 (image exposure) |
7 | Gnd |
8 | GPIO Out 2 |
GPIOs are decoupled by photocoupler. GPIO Out 1 by default provides an exposure sync signal with a logic high level for the duration of the image exposure. All GPIOs can be controlled via the IOControl module (IO and Projector Control). Pins of unsused GPIOs should be left floating.
Warning
It is especially important that during the boot phase GPIO In 1 is left floating or remains low. The rc_visard NG will not boot if the pin is high during boot time.
GPIO circuitry and specifications are shown in Fig. 7. The maximum rated voltage for GPIO In and GPIO Vcc is 30 V.
Warning
Do not connect signals with voltages higher than 30 V to the rc_visard NG.
Mechanical interface¶
The rc_visard NG offers a mounting-point at the bottom.
For troubleshooting and static applications, the sensor may be mounted using the standardized tripod thread (UNC 1/4”-20) indicated at the coordinate-frame origin. For dynamic applications such as mounting on a robotic arm, the sensor must be mounted with three M4 (metric standard) 8.8 machine screws tightened to 2.5 Nm and secured with a medium-strength threadlocking adhesive such as Loctite 243. Maximum thread depth is 6 mm. The two 4 mm diameter holes may be used for positioning pins (ISO 2338 4 m6) to ensure precise repositioning of the sensor.
Warning
For dynamic applications, the rc_visard NG must be mounted with three M4 8.8 machine screws tightened to 2.5 Nm torque and secured with threadlocking adhesive. Do not use high-strength bolts. The engaged thread depth must be at least 5 mm.
Coordinate frames¶
The rc_visard NG’s coordinate-frame origin is defined as the exit pupil of the left camera lens. This frame is called sensor coordinate frame or camera coordinate frame. An approximate location for the rc_visard NG is shown in the next image.
The mounting-point frame for the rc_visard NG is defined to be at the bottom, centered in the tripod thread, with orientation identical to that of the sensor’s coordinate frame.
Fig. 9 shows approximate offsets.
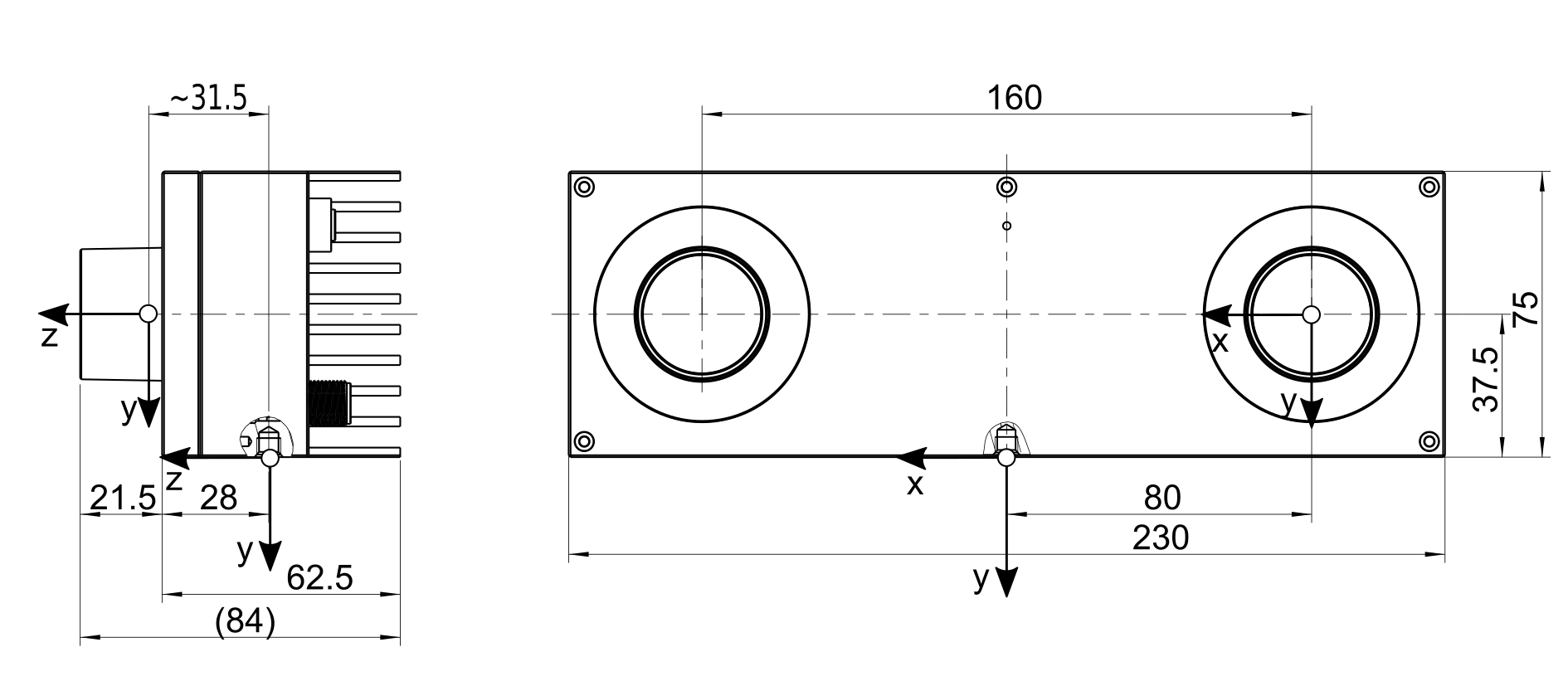
Fig. 9 Approximate locations of sensor/camera coordinate frame (inside left lens) and mounting-point frame (at tripod thread) for the rc_visard NG 160
Note
The correct offset between the sensor/camera frame and a robot coordinate frame can be calibrated through the hand-eye-calibration procedure.